Using Pomegranate in Eco Printing
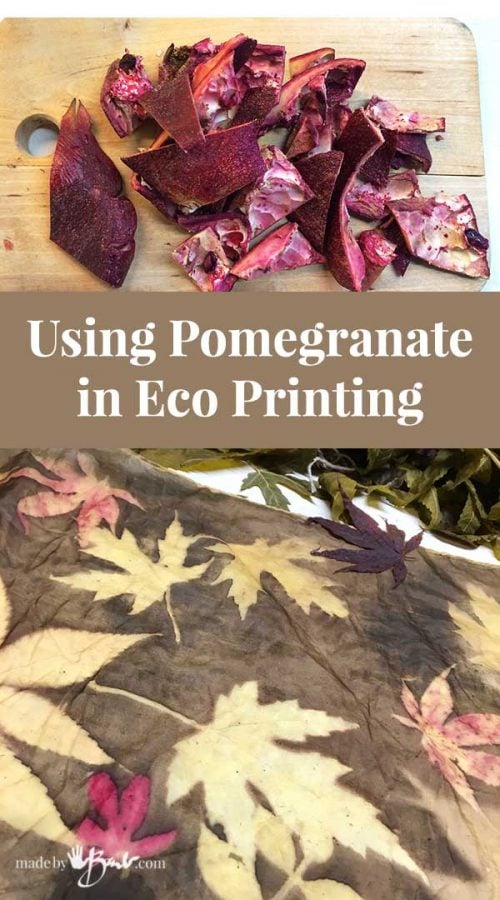
Is it not wonderful when you can use cast off ‘stuffs’ to create new beautiful ‘stuffs’?! That is one of the reasons I like this earthy art form so much. Using Pomegranate in Eco Printing opens a whole unique world of possibilities.

The Pomegranate Kitchen Scraps:
Sadly, Pomegranates don’t grow where I live but there are times where they are quite affordable. The tiny morsels of flavour are such a great edible treat and I make sure to get every last one, but the skins and pulp is what we use here.

Fill a (used for dye) pot with plenty of water to accommodate the easily chopped rinds and simmer. Generally speaking I try to keep temperatures down since many natural dyestuffs will lose some of their brightness when subjected to quite high rolling boils. ‘Slow and low’ will bring out the most from the matter. After as long a cook as you can handle (an hour and allow some cooling) you will need to strain it. I use old sheer curtain mesh and squeeze every drop out that I can.
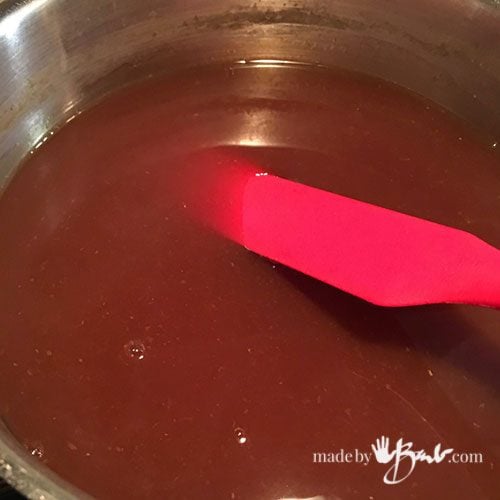
It shows a lovely warm red but that will not be the product since the major ‘gift’ from the Pomegranate is the tannins. As you may have found in this eco printing adventure the tannic acids in the leaves give us the results and Pomegranate is high in this.

The Eco Printing Process:
In my opinion here are no ‘definite’ rules to printing with botanicals. I am foremost an artist and less of a scientist so I do like to just ‘try-and-see-what-I-get’ most often. If this is all new to you you may want to check here for many of my instructions.

In this case I used an ‘iron blanket’ as a top layer over the placed leaves and an additional reused plastic barrier. The amount of iron will play a factor in how dark and dull the tones will be. Note the warm yellow that is imparted by the pomegranate.
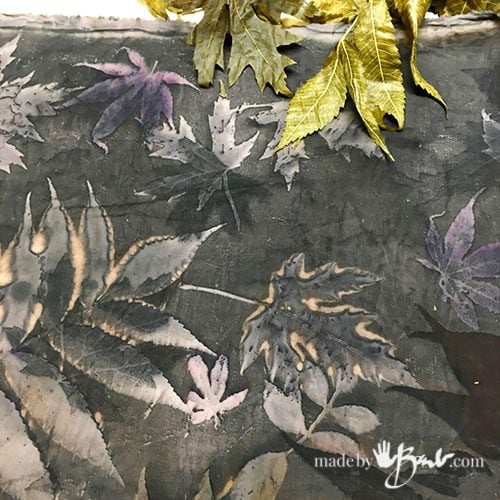
This is the print left on the iron blanket after the alternate steaming, as it was used multiple times; eventually it will be almost solid black. As you may noticed in all my eco printing iron plays a role in making the print permanent and iron loves to combine with tannin. Tannins also act as a mordant to help bind alum to cellulose (plant based) fibres. Sound complicated? Yes, for sure. I learn most from observing results of my tests.
The Magic Revealed:

I have learnt that ‘more’ tannins + ‘more’ iron = darker prints. Note the way that the leaves created a resist since they blocked the tannin and iron from combining. The reds are actually from the natural colour of the Japanese maples leaves. Adding alum into this process (before or after the tannin) will add an extra dose of golden yellow. How much you ask? Well that is always the question; there are some complex calculations of %’s against weight of fibre (WOF). I’m a ‘dash of this and dash of that’ kind of person…

After a vigorous wash, dry and iron it looks a wonderful taupe with buttery yellow shapes. A happy ‘accident’ of red maples just rounds it all off.

Won’t you brew up some of your rinds and let nature amaze you? I’ll warn you though; it may become addictive. Alright, gotta run and roll up some more bundles… because nothing is more fun than opening up and discovering the magic! Happy printing!
Let me know what wonders you’ve created.
yummy – so beautiful with the neutral greens you’ve used!
Thanks Brenda! I’ve yet to try the tumeric! It dyes too! Happy New Year!
I have a silk fabric that I painted with pomegranate and iron. How do I print something bright now?
done
Beautiful. I will definitely be trying this in the spring/ summer. Right now it is -22 degrees Celsius here in Montreal. Happy New Year.
Oh, I hear you! We just got a foot of snow! I’m working with my stock pile of dried leaves. Happy New Year!
I absolutely love this! You have me looking at kitchen waste as craft supplies, now.
Yesterday while out for a walk, I came across several eucalyptus branches that had been downed by a recent high wind storm. I may have to drive back over there and do some collecting. But where to store my haul…:-)
Oh, aren’t you lucky to find some euca as depending on the specie it can print red and orange! That will never happen here as we just got completely snowed in. Happy printing!
You eco prints are so gorgeous!!! And I love the fact that you make them with the use of discards! Keep them coming!
Can you explain the iron blanket? Your eco dye is beautiful!!
The iron is in solution (ferrous oxide) with water and the cloth (usually cotton for it’s absorbing capabilities) is soaked in it. Wring out before using in the bundle. Amount of wetness translates into how much iron and water is brought into the mix. Different fabric weights also make a difference. You can make iron water by having rusty things in water until the water turns rust colour, it is just had to gauge the strength, that’s what testing is for… have fun!
Hello, you do some really beautiful things and makes you want to leave to try them, but I do not clear visit you use the water of the pomegranate do you immerse the fabric in it or the leaves? Would the process be to bathe the leaves in the pomegranate and then in the iron before placing them on the fabric? Sorry, I’m sure it’s me, I don’t know. Not only do you do very beautiful things, you are also very generous to share them. Thank you
I dipped the silk fabric in the Pomegranate dye and then wrung out. The leaves are placed and an ‘iron blanket'(cotton fabric that is soaked in iron sulphate and then wrung out) is placed on top, then a layer of barrier (like plastic) and the rolled, tied. You may want to check out other posts Happy experimenting!
I do not understand the iron blanket or iron water part?
Mixing iron sulphate with water or using some rusty bits soaked in water makes the iron water. Using a fabric soaked with the iron water brings iron into the process (iron blanket). How concentrated makes for lighter or darker (sadder) prints. Hope that helps
Hello mam..how do we get yellow clr leaves ?? Nd what about leaves in which solution u dipped the leaves ??
In this procedure the leaves were not dipped. The fabric was dyed with the pomegranate dye and then the leaves were placed. I have described it in the post. The layer of an iron blanket makes the background darker so the leaves stay yellow from the pomegranate dye. Happy printing…
Hi
May i ask a question?
I do ecoprintig with eucalyptus but never getting red result and always it gets dark!!! Would you please help me?🙏🏻
That’s a tough one for me as it’s so hard to get any euca here. It does depend on the specie. I had a bit of one specie turn orange on some silk but it’s been hard to reproduce. I have read that it needs quite high heat and long processing as well as the right kind. Too much iron will ‘sadden’ it as well. I do think it prefers protein fibres. Good luck, hope that helps!
Hello, I have enjoyed reviewing your blogs on EcoDyeing. I have been doing this craft for a year. Still trying to figure it out. I do not see that you use water-vinegar solution to wet your fabric, such as the silk scarf or spray it to keep it wet. I am having what looks like large drops on the leaves and wonder whether it is from the spraying with the water-vinegar ( 1/1) solution. Also do you put any vinegar in your iron solution? I have used pomegranate and oak gal solutions after Alum mordanting, on the scarfs and linen, but feel when I use the Iron blanket it comes out too dark. I have changed the Iron solutions strength to 1/4 tsp in a quart of water but may need to dilute my tannin solutions further. Any recommendations on strengths of these would be helpful. Also do you wet your fabric prior to dipping in the tannins or the iron solutions. I have been scouring my scarfs, but the ones I order say they are “prepared for dyeing”, so I was thinking that I could leave the scouring out and just do the Alum mordanting. The water after scouring for 2 hours is pretty clear. Thanks for any words of wisdom, Karen.
Wow, lots of questions. I had much of the same questions and still do. Myself, I throw caution to the wind and sometimes just go for it! It’s really hard to specify exact measurements as it also depend on how thick and absorbant the fabric/blanket is as how much iron will come into play. I have used the same strength but different results on different fabric. I am a bit vary of using the vinegar in the iron water as some dyes are very PH sensitive like cochineal and logwood. I do tend to have the fabric damp before placing leaves, from a dye or rinse from mordant. I don’t scour bought silk scarves. I have not used Oak gall at all yet but do enjoy Myrobalan. . Don’t worry you will start to see patterns or develop a way that pleases you… Maybe take a workshop? I’m not set up to do them and currently too busy.