Magical Logwood Eco Printing
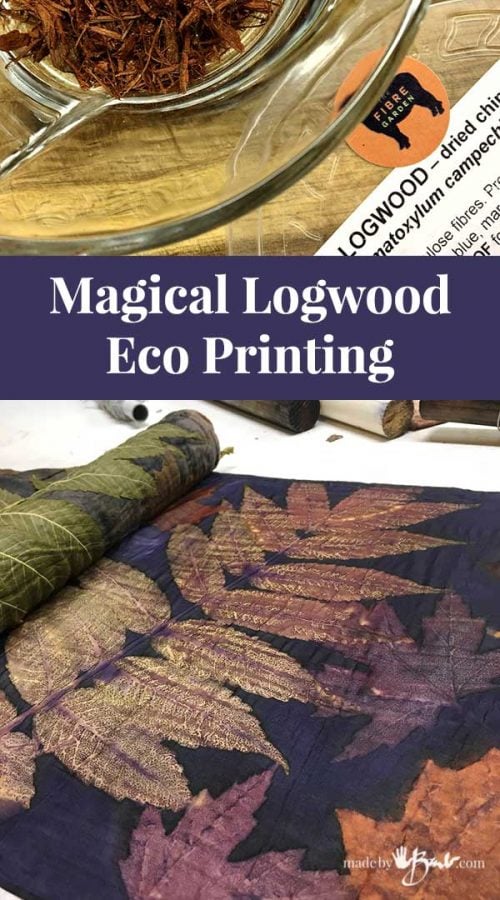
Just when I think I have seen all the magic I discover more! Nature keeps surprising us with it’s ability of making colour! How is it possible to make such wonder with some wood?! Magical Logwood Eco Printing has me in it’s grips right now…

Deceiving Looks:
Look at that! It just looks like some wood chips! This is Logwood; ‘Haematoxylum campechianum‘ and it’s abilities baffled me. This dye stuff can be bought in actual wood chips or as an extract. I used the more natural version of the wood chips which I bought at my local supply the Fibre Garden.

As with most natural dye products there are multiple ways of extracting the colour, but it is suggested to soak the logwood chips overnight to help with the hydration.

Oh What colour!
Whenever I use a new material, I am cautious about overheating it as many do not like to be over cooked. It quickly starts to leak out the amazing fuschia type dye.

A slow low simmer easily makes quite a strong amount of colour. It is suggested to use 20% – 50% weight of fibre (weigh the fabric). Yes, I know; I like to be experimental and just ‘wing it’ like an artist would… Make a container full and see how strong it looks.
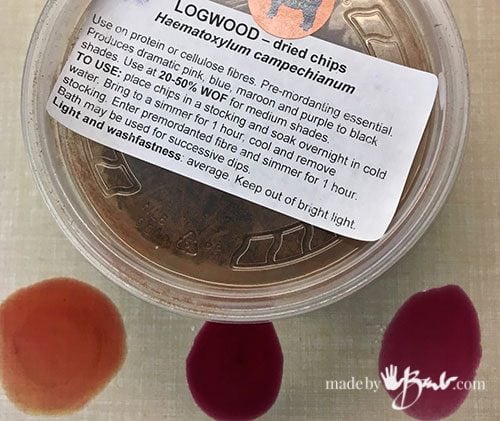
‘Playing’ with the dye can lead to some great things to observe! I’d much rather see how things react than read about them. Adding acids like vinegar (or citric acid solution) makes the dye more yellow and orange. Adding baking soda or washing soda forces it to become more purple. Such fun; I wish chemistry class would have had these kinds of tests then I would probably have been a chemist as well.
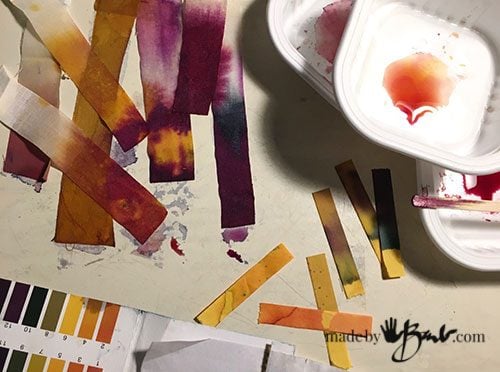
Little tests with cotton and silk gave a multitude of jewel tones! I may have just found my next favourite dye stuff! Litmus tests strips are handy to test the alkalinity of your own water as well as many other liquids for Eco Printing. I continually find that alkalinity plays a major role.
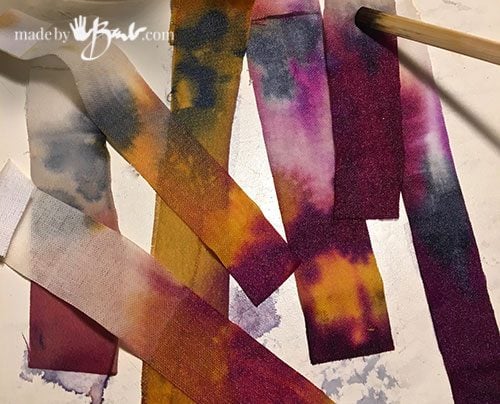
Such Magical Colours!
That ‘crazy artist brain’ sees beauty in the most odd places! I’m getting excited as there is some magic happening here.

This piece of silk was dipped in the cold dye for a short time (about 30 minutes) The silk was mordanted in alum and rinsed afterward as I was cautious about it’s alkalinity. Funny, the colour became more blue as it entered the dye! I would assume that the alkalinity of our water played a factor.

This little preview tells me it’s going to be amazing! An iron blanket was placed over the arranged favourite leaves and the tied bundle was processed in the microwave as has been my favourite lately for so many reasons!

Be still my heart!!! How can this even be possible from one dye colour?! Whenever a dye stuff reacts to alkalinity it then can produce so many variations according to the amount of tannic acids in the leaves used. Add in some of the variations of texture and TADA! Magic!

I also experimented by reversing the procedure and using the dye on a carrier blanket. This time the mordanted fabric is dipped in the iron solution. I love my maples and sumac leaves!

The quickly dyed carrier blanket brings the colour this time.

Such marvellous details, but be sure to wrap tightly.
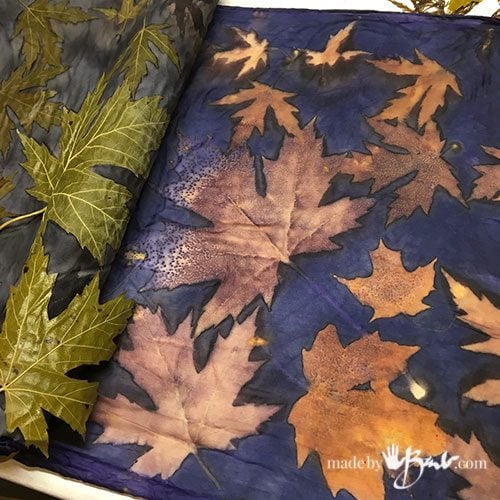
Mother nature keeps me guessing… how did that happen?! Why are there such little speckles on the maple leaf? ‘Mother Nature likes to keep secrets!’
But no matter what; I’m definitely going to see much Magical Logwood Eco Printing in my future! ‘and I hope you join me…
The colors you obtained are stunning. Last year I also used logwood with an iron blanket. Same results but six months later the purple had become a grey. Something to consider. Overdyed the whole thing with indigo and obtained a steel blue.
Interesting. I wonder if it reacted to something in the air or was it the iron… ‘Part of the magic I guess! I know my cochineal ones have been well over a year and are still the same and it is also a very PH sensitive dye.
Love the results!! Glorious colours.
Wow….that is sooo….beautiful Barb. I love the colors and I’m astonished by the way it all came out. I will have to definitely give this a try soon. Thank you for sharing.
All those years I used to paint pictures of nature meticulously and now it paints for me! Warms my heart!
I love your work! This turned out so nice! I think I like the iron blanket one the best.
I confess too that the iron blanket method gives such nice definition! Then I also feel the precious dye is on the fabric for sure! Happy printing!
Oh jeez! Now I have to order more dye!! So inspiring….❤❤❤
Yes, maybe there is a shop nearby or Logwood grows near you! I’d be happy with that! Logwood can be such a chameleon colour!
Our ecoprinting success has recently blossomed thanks to your generous sharing. Thank you so much!
Logwood scarf—Did you first dye the scarf with logwood, then add leaves and then cover with the iron blanket? Or iron/myrobalan blanket? Did the leaves discharge some of the dark logwood color or was the base color a lighter gray/blue logwood which darkened around the leaves by the blanket?
And could you talk a little more about the effects of a higher alkaline bath.
Again, thanks so much. You’re wonderful. Caroline
I’m glad you are happy with results! On one of the scarves it was dyed first and then the leaves discharged the dark logwood colour similar to what happens with cochineal. It probably is a reaction to the tannic acids in the leaves. It can also be a weaker dye and pronounce the outline with the iron blanket. An alkaline bath may alter the direction of the colour. I’ll have to try that… so many tests! Let me know how it goes.
Love this and will definitely try. I’m a newbie and have had my share of failures… maybe logwood is the ticket! I love your results … rich colors and such crisp leaves… fantastic!
Failures… I remember! Much has to do with mordant, fabric/fibre, iron, and choice of leaves. You will get there! AND if it doesn’t work first time, it can be printed again and again…
I have over printed a shirt A couple of times and now just looks a mess 😩I would like to re dye and print again and see if I can get some nice clear leaves. Will the original mordanting Of AA interfere with the outcome and is there a way to re mordant say with Soy to try and get a pattern instead of just blotches. Thank you for any help, love your info and your Barb. .
Once mordanted – always mordanted. Maybe a lightening with some citric acid solution and then good rinse, dye again. Maybe consider your bundling tightness and also your choice of leaves. Many factors play together. Don’t despair…
Just beautiful! Can you please provide more information on how you used the Logwood dye in the carrier blanket? What was the fiber content of the carrier blanket? Did you mordant the carrier blanket or just soak the fiber in the Logwood dye? Thank you for sharing your knowledge with us.
Thanks! There will soon be a post about ‘carrier blankets’. I suppose you already are aware of the iron blanket method?
Thank you for your generous sharing and wonderful posts. I am still trying to learn about this iron blanket-tannin blanket process since the formulas seem to be somewhat “protected” like the recipe for the Colonel’s chicken!
Yes, I know since I had to crack the secret codes myself as I am all self taught in eco printing. It involved many, many, probably hundreds of test runs! That’s why they don’t share for free. I’m amazed when I get complaints that there are ads on my site… since the content is free. Anyways, the iron ‘blanket’ is an easy way to get good definition with most prints. It’s my go-to method in most cases even with a pre-dyed fabric like cochineal or madder. The dye carrier is much the same but I have not made a post yet. It is in the works. Happy printing!
My first attempt with an iron blanket was less than successful. It turned the material very dark. What dilution do you suggest for the iron water ?
Yes, that’s always the question. If using iron sulphate less than a teaspoon per bucket is best. But there are other factors like how much fabric, density of it, your water, leaves etc that will effect the outcome. I work like an artist, not a chemist with crazy measuring. Iron to WOF (weight of dry fibre) can be 1%. I usually go by feel/look. That’s why you should do some testing and take notes… Citric acid solution will lighten dark iron, but watch carefully.
I love your work and have learned a great deal from your many posts. I have a long history of marbling silk scarves using silk charmeuse and would like to do more with eco printing on silk. When working with scarves, what silk do you prefer working with? There are several options with habotai, charmeuse, crepe, and I wonder if some are better than others for this specific type of work.
If you have had access to the better quality silks I do notice they take colour even better. I have used the habotai mostly since it was inexpensive enough to experiment. I have some up-cycled satin (I think) and have tried the crepe and loved both of them. Other eco printers I know have success on all of them even on mixes with wool since it’s also a protein fibre. Be ready to experiment with whatever you try… Good Luck
Lindo !!… Amo seu trabalho.